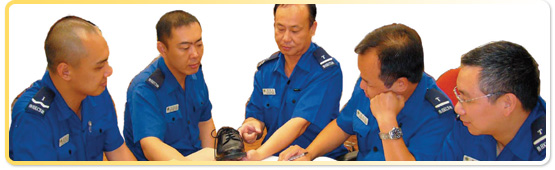 |
Occupying prisoners in a regime of regular purposeful work would oblige them to structure their time spent in prisons, and make them less prone to disruptive activities. Engaging prisoners in purposeful work would cast positive impacts on their rehabilitation programmes and reintegration into the society. Purpose work carries manifest and latent functions for the Department and the prisoners.
The labour derives from prisoners' purposeful work represents a valuable manpower resource to society. This Chapter outlines the work done by the Correctional Services Industries in directing the prisoner's purposeful work towards the supply of products and services to the community in the year 2006.
Wilfred MA
General Manager (CSI)
 |
Instructor instructs an inmate in making wooden yacht models. |
|
 |
Prisoners fabricate road signs in sign-making workshop. |
|
The concept of work plays an important part in managing prisoners. The work of the Correctional Services Industries (CSI) contributes to the Department's mission in keeping prisoners in a secure, safe and humane environment through securing purposeful work from the public sector market to occupy the prisoners and spare them from idleness or monotony.
The work of the prisoners is directed towards the production of goods and services for the community in a cost-effective manner. Our customers in the community are public bodies which include government departments, financially autonomous public bodies and charitable organisations. The commercial value of goods and services provided by CSI to these public bodies in 2006 was $444.3 million. A breakdown of commercial value by trade is at Appendix 19. |
Employment of Prisoner/Inmate
In the year under review, an average of 6 277 prisoners were employed in 13 different trades in more than 150 industrial workshops. The other prisoners were engaged in essential domestic duties including cleaning, kitchen and maintenance work.
Garment trade continued to provide the highest employment opportunities to more than 2 400 prisoners on the average. Other trades with high employment included laundry, envelope making and bookbinding. A breakdown of the employment by trade as at 31 December 2006 is at Appendix 20.
High proportion of short-term prisoners and high prisoner labour turnover rate continued to be the greatest challenges to CSI. The short-termers drove up the demand for simple jobs, and the high turnover rate was not conducive to labour skill retention. Process re-engineering and workplace engineering were being carried out in our workshops to cope with the challenges.
|
Marketing and Business Environment
CSI is not immune from business competitions to compete for orders from the public sector market. New initiatives such as total outsourcing and Public Private Partnerships (PPP) instituted by government departments have changed the business environment in the public sector market. CSI has to expand its marketing efforts to cover not only government departments, but to include their outsourcing contractors and the PPP partners as well.
CSI has to compete for business beyond price. Value chain analyses were conducted to provide value-added services to our customers. The value chain analyses had precipitated quite a number of business initiatives. These initiatives include design services such as the application of performance fabric to achieve better value-for-money uniform; vertical integration of CSI products and services, for example the integration of hospital linen supply and laundry service, to minimise the administrative overhead of our customers; and business process re-engineering opportunities to streamline our manufacturing and business process flows to cope with the market demand on small-batch and quick-response orders. |
Facility Management
We had adopted a strategic approach to manage the facilities in the prison workshops. We pegged our facility management work with the Department's initiatives on redevelopment of existing correctional facilities and the in-situ reprovision of institutions. In planning the acquisition of new facilities to replace the worn out ones, we had also included elements such as market trend and prisoner profiles into our consideration. For example, tunnel finisher were planned to replace the worn out flat buck presses in our laundry to cope with the sharp increase in working dress press work demand by the public hospitals after the SARS saga. This kind of facility planning work had been extended to cover the Hospital Authority's laundries contracted to us for operation under Service Level Agreements.
The new Lai Chi Kok Correctional Institution was fitted with two garment workshops. Bearing in mind the market demand on filter masks and the profile of female prisoners in this institution, we had secured capital funding approval to setup a second filter mask production line in this institution to create more purposeful work opportunities for the prisoners on the one hand, and on the other hand to increase our supply of Hong Kong Q-Mark licenced filter masks to the public sector market.
Improvement and re-layout work on the shoe-lasting section of the shoe-making workshop in Stanley Prison were completed in May 2006 after a four-month renovation work. The foregoing works had given renewed impetus to the shoe-making workshop for more order opportunities.
Apart from the ventilation improvement work conducted in the fibreglass workshops in September 2006, the metal workshop in Ma Po Ping Prison and Tong Fuk Centre was closed in early October for renovation work. The layout of this workshop would be revamped with upgraded equipment for better workflow and new metal product lines. |
Quality Management
We continued to commit in timely delivery of quality products and services. Renewal audits had been conducted by the Hong Kong Quality Assurance Agency (HKQAA) on the two ISO 9001 certified sign-making workshops and four laundries, and by the Federation of Hong Kong Industries on one Q-Mark certified filter masks workshop. All of them passed the surveillance audits without any non-compliance detected.
Apart from benchmarking the international standards and best practices, we kept on improving our Quality Management System. The applications of Quality Assurance Committees, Process Improvement Teams and Quality Control Circles quality management tools were impressed upon the industrial staff to drive for continuous quality improvement. |
Application of Information Technology
We have been applying information technology (IT) intensively in our work to cope with the voluminous monitoring and quick-response work arising from the aforementioned initiatives.
Computerised tracking system was developed and deployed to keep track of the library books sent to our workshops from the Leisure and Cultural Services Department for lamination. Development work on this kind of computerised tracking system were being extended to cover the tracking of uniform items sent to us from the Hospital Authority and the Department of Health for laundering and pressing. We had also expanded our Manufacturing Management and Control System network to include prison workshops for efficient industrial operations to cope with quick response orders. We had also leveraged our IT system as a value-added service to our customer, for example, e-ordering, and on-line stock-level and order progress enquiries.
|
Staff Training and Staff Development
The foregoing initiatives and hardware facilities were matched with training and development programmes to enhance the knowledge and skills of our industrial staff. In addition, these programmes were employed as a communication tool to impress upon the missions and values of CSI to the industrial staff.
In the year 2006, we had conducted about 50 training and development programmes to more than 200 industrial staff. External institutions such as the University of Hong Kong and the Hong Kong Polytechnic University were engaged to conduct these programmes in order to enhance not only the job-wise technical knowledge and skills of industrial staff, but also to promote their awareness on the challenges facing CSI. |
Occupational Safety and Health
We placed overriding emphasis on Occupational Safety and Health (OSH) at work not to meet our obligations to staff, but also a realisation to our mission in detaining persons committed to our custody in a safe environment. This was implemented through promotion campaigns, risk assessments, and continuous improvement to the working environment.
Among the OSH initiatives conducted in 2006, we had engaged the Department and HKQAA to organise a customised Safety Review Course to more than 20 officers, which qualify them to conduct Safety Management System review for their institutions proficiently. Seminars and training courses on OSH were also arranged for all grades of staff in all our institutions.
|
|